Резка металла своими руками
Каждому промышленному предприятию либо частному лицу, которое занимается металлообработкой, требуется станок для резки металла, что отвечает заданным требованиям к цене, безопасности и производительности. Сейчас выделяют много различных способов обработки металла — обработка металла плазмой, давлением и лазером, и ручная резка металла ножницами.
Если вы ещё не определились с подходящим оборудованием и оптимальным методом для резки металла, отечественная статья окажет помощь вам сделать это.
Самый распространенными и действенными с экономической позиции на сегодня выступают такие способы, как плазменная, лазерная и газовая резка. Частенько металл режут пресс-ножницами, каковые способны пробивать отверстия и пазы различных форм в стали разнообразной прочности.
При выборе одного способа обработки металла из вышеперечисленных рекомендуется ориентироваться на уровень качества самого процесса работы, количество конечных отходов и точность выполнения. Серьёзным моментом выступает и возможность создания маленькой партии подробностей в максимально сжатые строчки при оптимальной цене резки на профильных производствах.
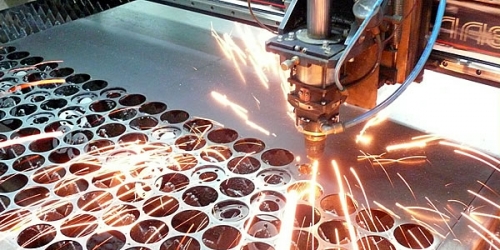
Более, того выбор одного из них оправдан при учете определенных параметров, таких как эффективность работы, конечный итог, цена изделия. Наряду с этим существует определенный перечень сплавов и металлов, с которыми целесообразно трудиться тем либо вторым оборудованием.
Газовая резка металла Газовая резка является процессом резки железных изделий, что основан на свойстве металлов, что нагреты до определенной температуры (1200-1300 градусов), гореть в чистом кислороде. Благодаря газовой резке листового металла в наши дни возможно осуществлять различные типы обработки — подготовка кромок для процесса сварки, прямая резка металла, процедура резки под углом.
Сущность разработки Резку принято затевать с кромки страницы. Поверхность, что предназначена для резки, нужно очистить от ржавчины, грязи и окалины. газ и Кислород в горелки подается из баллонов, где они находятся в сжатом состоянии.
Масса одного баллона равняется 70 кг. Рабочее давление кислорода на один метр квадратный образовывает 300 кН, а газа — достигает 50 кН.
Давление наряду с этим возможно отрегулировать в редукторе устройства, что навинчен на штуцер кислородного баллона. Редуктор оснащен манометром большого давления, что показывает давление кислорода в баллоне, и оборудован манометром низкого давления, что предоставляет данные о рабочем давлении.
Лист металла прожигается и разрезается струей кислорода, которая подается под громадным давлением. Образующиеся окислы железа вытекают в расплавленном состоянии и выдуваются из полости реза.
Разработка газовой резки металла предполагает применение резака, что представляет собой некую сварочную горелку со особым устройством для подвода кислорода. Виды газовой резки В данном виде сварки традиционно употребляются водород (коксовый, нефтяной и природный) и ацетилен, пары бензина и керосина, каковые могут быть около в ходе горения температуры в 3200 градусов.
Зависимо от используемого горючего газа, выделяют водородно-кислородную, ацетиленокислородную и бензинокислородную резку, и машинную и ручную резки. Отдельным видом газовой резки выступает флюсокислородная резка, что разрешает разделять тяжело поддающиеся резке металлы — хромоникелевые и высокохромистые стали, чугуны и алюминиевые сплавы.
В этом случае процедуру облегчают порошкообразные флюсы, каковые вдуваются вместе с кислородом. Кроме разделительной кислородной резки, в то время, когда режущая струя фактически перпендикулярна поверхности металла, применяют кислородную обработку, в ходе которой режущую струю направляют к поверхности металла под острым углом.
Данным методом режут страницы из углеродистых средне- и низколегированных сталей, каковые имеют толщину от 1 до 200-300 миллиметров. На видео о газовой резке металла вы заметите, что вероятной считается газовая резка стали толще 2 метров.
Кислородная резка обширно употребляется в цветной и тёмной металлургии, а также в частном постройке. Предъявляемые требования Дабы совершить этот процесс, нужно выполнить ряд условий.
Не забывайте, что металл обязан владеть большей температурой плавления, чем показатель температуры горения в кислороде. Наоборот, оксиды металла должны различаться температурой плавления меньшей, чем температура плавления выбранного металла.
Следите, дабы уровень термального действия был достаточен для обеспечения непрерывности процесса резки. Обрабатываемый металл не должен владеть через чур высокой теплопроводностью, поскольку в другом случае тепловая энергия будет скоро отводиться.
Соответственно данным параметрам, каковые предъявляются к газовой резке, для данной процедуры идеально подходят низкоуглеродистые и железо и низколегированные стали. Преимущества газовой резки Главным преимуществом газовой резки металла есть возможность раскроя страниц металла, каковые имеют громадную толщину — до 200 миллиметров.
Наряду с этим ширина среза образовывает 2-2,5 миллиметров. При помощи оборудования для газовой резки металла возможно совершить вертикальную кромку среза, что на протяжении процесса не будет закаливаться.
Нельзя не отыскать в памяти и об экономической эффективности данной разработке — газовая резка не требует вложения громадных денежных средств. Минимальны требования, что связаны с техобслуживанием процесса.
Несомненным преимуществом газовой сварки металла есть и тот факт, что для её проведения не нужна никакая механическая обработка. Плазменная резка металла Резка металлов с применением струи плазмы вместо резца именуется плазменной.
Поток плазмы формируется в следствии обдува сжатой электрической дуги газ, что нагревается и в ходе ионизируется — распадается на положительно и отрицательно заряженные частицы. Плазменный поток в большинстве случаев имеет температуру близко 15 тысяч градусов Цельсия.
Методы плазменной резки Выделяют поверхностную и разделительную плазменную резки. Но на практике широкое применение взяла как раз разделительная разработка резки металла. Сам процесс резки реализовывают двумя способами — плазменной струёй и дугой.
При резке металла плазменной дугой он включается в электрическую цепь. Вышеупомянутая дуга появляется между электродом резака и изделием из вольфрама. Если вы выбрали вторую методику, то не забывайте, что в резаке дуга формируется между двумя электродами.
Разрезаемый лист не включается в электрическую цепь. По производительности плазменная резка превосходит кислородную. Но в случае если вам необходимо порезать титан либо металл громадной толщины, то рекомендуется дать предпочтение кислородной резке.
При резании цветного металла плазменная резка считается незаменимой. Особенно это относится алюминия. Аппараты для плазменной резки Для образования плазмы принято применять активные и неактивные газы.
К первой группе относят кислород и воздух, каковые употребляются при резке тёмных металлов (меди, алюминия и стали), и неактивные — водород, азот и аргон для цветных металлов и резки сплавов (высоколегированной стали, которая имеет толщину до 50 миллиметров, латуни, меди, титана и алюминия). Для механизации процедуры были созданы аппараты для резки металла — полуавтоматы и переносные автомобили различных модификаций.
Полуавтоматы трудятся с неактивными и активными газами, тогда как переносные автомобили применяют только сжатый воздушное пространство. Резка металла плазмой дома осуществляется при помощи ручных аппаратов, в набор которых входят режущий плазмотрон, коллектор, кабель-зажигалка и шланговый пакет, предназначенная для возбуждения режущей дуги.
Такие наборы разрешают делать ограниченный объем работы с загрузкой оборудования не больше чем на 50%. Исходя из этого их рекомендуется укомплектовать на время работы выпрямителями и сварочными преобразователями.
Сущность разработки Началом процедуры резания металлов есть момент, в то время, когда возбудилась плазменная дуга. Начав резку, направляться поддерживать между соплом плазмотрона и поверхностью металла постоянное расстояние, которое образовывает 3 — 15 миллиметров.
Стремитесь к тому, дабы ток был минимальным в ходе работы, по причине того, что при увеличении силы расхода и возрастании тока воздуха падает сопла работы плазмотрона и ресурс электрода. Но уровень тока наряду с этим обязан снабжать высокую производительность резки. Самой сложной операцией выступает пробивка отверстий, поскольку вероятно образование двойной дуги и выход плазмотрона из строя.
Не забывайте, что инструмент для резки металла при пробивке обязан над поверхностью подробности подниматься на 20 — 25 миллиметров. В рабочее положение плазмотрон опускается по окончании того, как лист будет полностью пробит.
Если вы пробиваете отверстия в страницах, каковые имеют громадную толщину, рекомендуется применять защитные экраны, имеющие отверстия диаметром 10-20 миллиметров. Экраны нужно помещать между изделием и плазмотроном.
При резке алюминия с применением аргоноводородной смеси для повышения стабильности горения дуги содержание водорода не должно быть больше 20%. Резку меди принято делать с применением водородосодержащих смесей. Латунь испытывает недостаток в азотоводородной смеси либо азоте.
По окончании резки медь обязательно необходимо зачистить на глубину 1-1,5 миллиметра. Но не это требование совсем не обязательно для бронзы.
Лазерная резка металла Резка лазером есть принципиально новым видом обработки металла, что отличается очень производительностью и высокой точностью. Подобные режущие станки в мире металлообработки совершили революцию, сделав процедуру создания сложных железных конструкций несложнее, стремительнее и дешевее по цене.
Лазерная резка в наши дни с уверенностью вытесняет другие разновидности обработки железных заготовок и делается все более популярной. Сущность разработки Разработка лазерной резки металла собственными руками на сегодня — одна из самых прогрессивных разработок в создании различных подробностей из листовых материалов.
Процедура хороша собственной универсальностью, по причине того, что она разрешает трудиться с любыми материалами — железного и неметаллического происхождения. Лазерный луч есть узконаправленным световым потоком мелкого диаметра, что владеет высокой интенсивностью.
В случае если лазерный луч навести на железную поверхность либо второй жёсткий объект, изделие нагреется до большой температуры. Её достаточно, дабы металл начал плавиться в точке контакта. Но вместе с этим участки поверхности, каковые прилегают к лучу, остаются тёплыми, но не повреждаются.